TEEXMA®
for
Quality
Support your quality approach and processes
TEEXMA®
for
Quality
Support your quality approach and processes
CUSTOMER SUCCESS
CUSTOMER SUCCESS
OPERATING SCOPE
OPERATING SCOPE
Achieve market-expected quality by proactively anticipating, effectively controlling, and proficiently mastering your quality processes.
Achieve market-expected quality by proactively anticipating, effectively controlling, and proficiently mastering your quality processes.
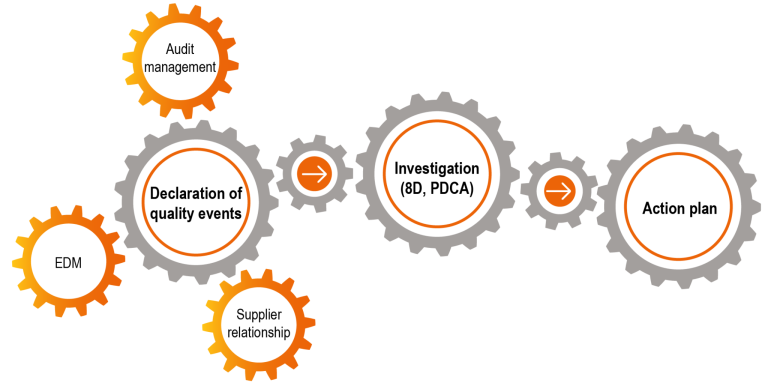
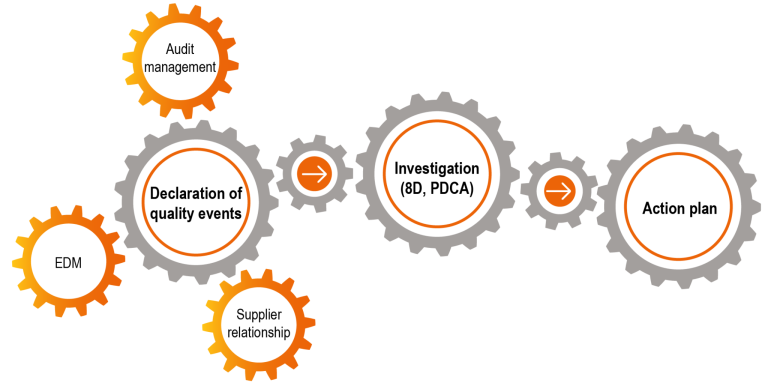
WHY CHOOSE TEEXMA® for Quality
WHY CHOOSE TEEXMA® for Quality
CERTIFICATION
Respond to ISO 9001, ISO 14001, EN9100, 19011
IDENTIFY
Analyze errors and identify root problem
COMMUNICATE
Enhance communication effectiveness with suppliers.
UNIFY
Formalize indicators and reports of the quality process
REDUCE
the occurrence of nonconformities
MONITOR
Closely monitor action plan
CENTRALIZE
the management of quality actions
ANTICIPATE
risks and opportunities
CERTIFICATION
Respond to ISO 9001, ISO 14001, EN9100, 19011
IDENTIFY
Analyze errors and identify root problem
COMMUNICATE
Enhance communication effectiveness with suppliers.
UNIFY
Formalize indicators and reports of the quality process
REDUCE
the occurrence of nonconformities
MONITOR
Closely monitor action plan
CENTRALIZE
the management of quality actions
ANTICIPATE
risks and opportunities
TEEXMA® for Quality supports you with:
TEEXMA® for Quality supports you with:
Coordinate quality incidents
Effectively handle and guarantee the traceability of deviations, customer grievances, and enhancements promptly.
Connect incidents with a repository of defects and data from your product lifecycle management (PLM) or enterprise resource planning (ERP) system.
Arrange events based on their significance and urgency.
Automatically notify the relevant users via email.
Record events conveniently through the mobile application from any location.
Performing inquiries
Conduct thorough investigations using user-friendly processes like the Eight Disciplines of Problem Solving (8D) or the Plan-Do-Check-Act (PDCA) cycle.
Identify issues utilizing the 5W1H questioning method (Who, What, When, Where, Why, and How).
Analyze underlying causes by employing an Ishikawa diagram.
Action plan management
Managing documentation
Collect all quality-related documentation (e.g., certificates, standards, procedures, reports, etc.) using electronic document management (EDM).
Version, archive, validate, and distribute documents based on a customizable workflow with electronic signatures.
Utilize keyword searches to locate specific content within documents, leverage advanced search tools, subscribe to content types, and manage access rights and mailing lists.
Overseeing audits
Organize audits by aligning them with specific themes and control points related to procedures and compliance criteria.
Allocate resources and establish deadlines for audit activities.
Design structured internal audit forms.
Supervising supplier quality
Establish communication channels with suppliers via a secure external portal.
Automatically track and follow up with suppliers regarding their eligible documents, action plans, and responses to claims.
Assess supplier performance using customizable indicators.
Conducting FMEA risk analysis
Capture, organize, and maintain design data consistency throughout the entire design process.
Effectively manage the project team’s activities and generate summary and statistical documents automatically.
Leverage accumulated knowledge through comprehensive generic studies.
Overseeing enterprise risk
Supervise business risks and opportunities in compliance with multiple quality assurance reference standards, including:
- ISO 9001 (Quality Management)
- ISO 14001 (Environmental Management)
- IATF 16949 (Automotive Quality Management)
- ISO 13485 (Medical Devices)
- EN 9100 (Aerospace Quality Standards) And others…
Additionally, manage action plans effectively.
Performing functional analysis
Utilize visual functional modeling tools like Octopus, Cross Sorting, FAST, and others.
Organize and reuse functional specifications while maintaining traceability of modifications.
Coordinate quality incidents
Performing inquiries
Action plan management
Effectively handle and guarantee the traceability of deviations, customer grievances, and enhancements promptly.
Connect incidents with a repository of defects and data from your product lifecycle management (PLM) or enterprise resource planning (ERP) system.
Arrange events based on their significance and urgency.
Automatically notify the relevant users via email.
Record events conveniently through the mobile application from any location.
Conduct thorough investigations using user-friendly processes like the Eight Disciplines of Problem Solving (8D) or the Plan-Do-Check-Act (PDCA) cycle.
Identify issues utilizing the 5W1H questioning method (Who, What, When, Where, Why, and How).
Analyze underlying causes by employing an Ishikawa diagram.
Enact prompt corrective and preventive measures for each root cause.
Oversee, track, and assess actions through dashboards in a unified reference system.
Generate reports automatically.
Managing documentation
Overseeing audits
Supervising supplier quality
Collect all quality-related documentation (e.g., certificates, standards, procedures, reports, etc.) using electronic document management (EDM).
Version, archive, validate, and distribute documents based on a customizable workflow with electronic signatures.
Utilize keyword searches to locate specific content within documents, leverage advanced search tools, subscribe to content types, and manage access rights and mailing lists.
Organize audits by aligning them with specific themes and control points related to procedures and compliance criteria.
Allocate resources and establish deadlines for audit activities.
Design structured internal audit forms.
Establish communication channels with suppliers via a secure external portal.
Automatically track and follow up with suppliers regarding their eligible documents, action plans, and responses to claims.
Assess supplier performance using customizable indicators.
Conducting FMEA risk analysis
Overseeing enterprise risk
Performing functional analysis
Capture, organize, and maintain design data consistency throughout the entire design process.
Effectively manage the project team’s activities and generate summary and statistical documents automatically.
Leverage accumulated knowledge through comprehensive generic studies.
Supervise business risks and opportunities in compliance with multiple quality assurance reference standards, including:
- ISO 9001 (Quality Management)
- ISO 14001 (Environmental Management)
- IATF 16949 (Automotive Quality Management)
- ISO 13485 (Medical Devices)
- EN 9100 (Aerospace Quality Standards) And others…
Additionally, manage action plans effectively.
Utilize visual functional modeling tools like Octopus, Cross Sorting, FAST, and others.
Organize and reuse functional specifications while maintaining traceability of modifications.
BENEFITS
BENEFITS
Enhanced product quality
Achieve comprehensive quality assurance by eliminating the underlying causes of nonconformities and proactively addressing risks.
Achieve cost reduction through process optimization and automation.
Lowered expenses
Attained regulatory compliance
Establish the necessary quality procedures to align with the standards and regulations’ requirements.
Establish the necessary quality procedures to align with the standards and regulations’ requirements.
Enhanced customer satisfaction
Enhanced product quality
Lowered expenses
Attained regulatory compliance
Enhanced customer satisfaction
TEEXMA® for Quality in Industry :
TEEXMA® for Quality in Industry :
Transportation
Quality management in vehicle production encompasses diverse areas across automotive, aerospace, railway, and naval sectors.
Our solution empowers you to maintain comprehensive control over your quality processes within sectors characterized by highly technical products, extended product life cycles, and small series production.
Ensure compliance with safety requirements and minimize production and passenger risks.
Energy
TEEXMA for Quality supports electrical, nuclear, and renewable energy industries in quality control.
Improve performance and safety by efficiently addressing non-conformities.
Manage corrective and preventive actions with configurable workflows and mobile app support.
Attain complete traceability and capitalize on experience for optimized quality processes.
Health
In the healthcare field, there exist approximately 1400 standards, with certification/accreditation and quality management being key concerns.
We provide assistance in enhancing your quality and compliance processes, whether you are a pharmaceutical company working with the ISO IDMP series, a medical device company following the ISO/TC210 standards, or a healthcare center.
Manufacturing
Quality concerns in industrial companies encompass a wide range of objectives, including enhancing customer satisfaction, optimizing production processes, and improving overall product quality.
Whether your goal is ISO 9001 certification or improving operational efficiency, TEEXMA® for Quality is here to support your quality management endeavors.
Our solution is trusted in various sectors, spanning from mechanical components to chemicals, and from raw materials to luxury goods.
Laboratories
Efficient organization of a laboratory is crucial. Consolidate all quality procedures pertaining to your laboratory in an internal and external document repository.
TEEXMA® for Quality offers tailored support for quality control and R&D laboratories, enabling structured management of incidents and CAPA (Corrective and Preventive Actions).
Address the ISO 17025 standard requirements effortlessly by managing non-conformity events related to materials or equipment and associating them with tests or samples.
Transportation
Quality management in vehicle production encompasses diverse areas across automotive, aerospace, railway, and naval sectors.
Our solution empowers you to maintain comprehensive control over your quality processes within sectors characterized by highly technical products, extended product life cycles, and small series production.
Ensure compliance with safety requirements and minimize production and passenger risks.
Energy
TEEXMA for Quality supports electrical, nuclear, and renewable energy industries in quality control.
Improve performance and safety by efficiently addressing non-conformities.
Manage corrective and preventive actions with configurable workflows and mobile app support.
Attain complete traceability and capitalize on experience for optimized quality processes.
Health
In the healthcare field, there exist approximately 1400 standards, with certification/accreditation and quality management being key concerns.
We provide assistance in enhancing your quality and compliance processes, whether you are a pharmaceutical company working with the ISO IDMP series, a medical device company following the ISO/TC210 standards, or a healthcare center.
Manufacturing
Quality concerns in industrial companies encompass a wide range of objectives, including enhancing customer satisfaction, optimizing production processes, and improving overall product quality.
Whether your goal is ISO 9001 certification or improving operational efficiency, TEEXMA® for Quality is here to support your quality management endeavors.
Our solution is trusted in various sectors, spanning from mechanical components to chemicals, and from raw materials to luxury goods.
Laboratories
Efficient organization of a laboratory is crucial. Consolidate all quality procedures pertaining to your laboratory in an internal and external document repository.
TEEXMA® for Quality offers tailored support for quality control and R&D laboratories, enabling structured management of incidents and CAPA (Corrective and Preventive Actions).
Address the ISO 17025 standard requirements effortlessly by managing non-conformity events related to materials or equipment and associating them with tests or samples.