TEEXMA®
for
Additive Manufacturing
The end-to-end solution from R&D to production
TEEXMA®
for
Additive Manufacturing
The end-to-end solution from R&D to production
OPERATING SCOPE
OPERATING SCOPE
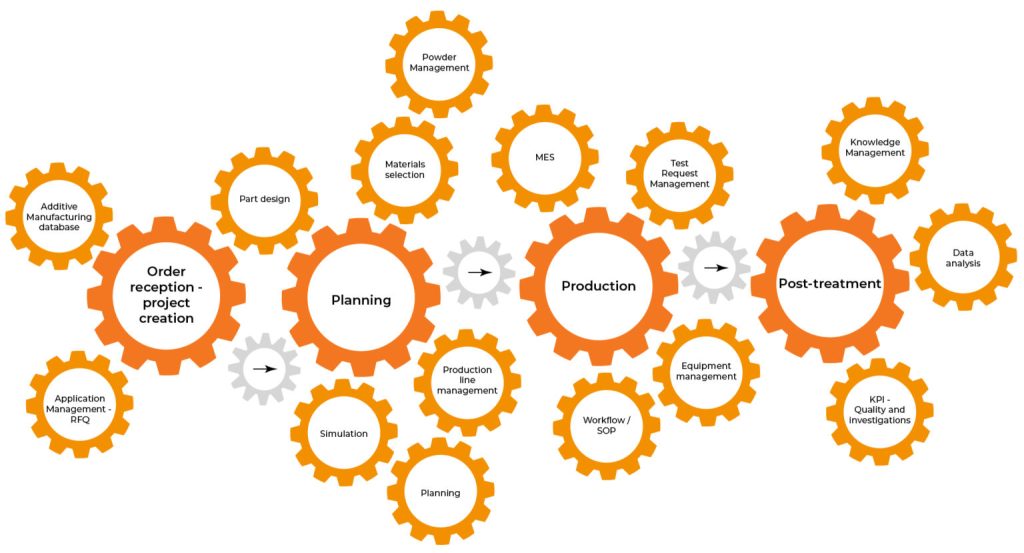
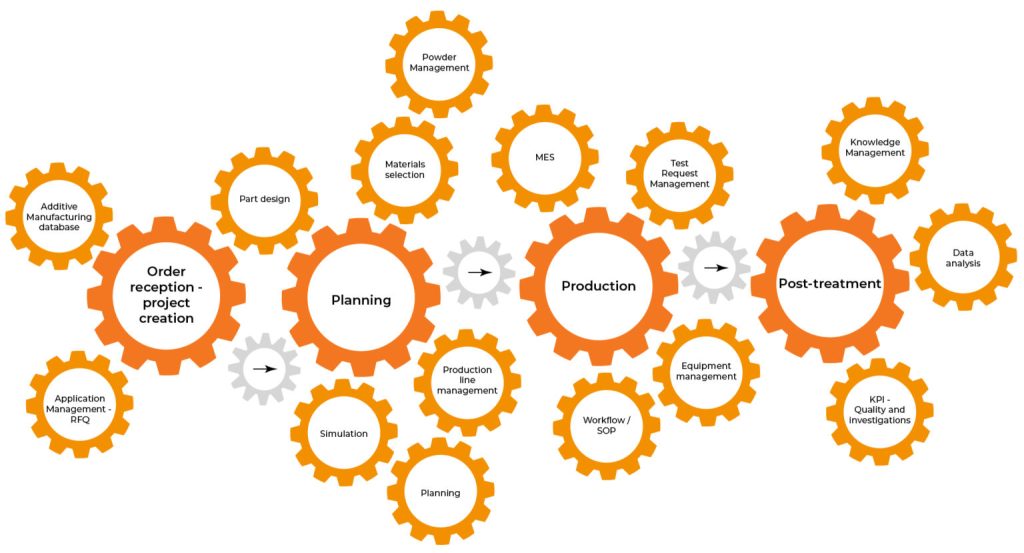
WHY CHOOSE TEEXMA® for Additive Manufacturing
WHY CHOOSE TEEXMA® for Additive Manufacturing
TRACE
from raw materials to completed parts
MANAGE
a raw material database including metal powder, polymer coils, and more.
ADAPT
Adjust data traceability.
LEVERAGE
Extract and capitalize reports
DEFINE
The processes and machine parameters of additive manufacturing.
CHARACTERIZE
The materials throughout every stage of transformation.
ENSURE
the privacy and security of your data.
MANAGE
Enhance finished product quality through nonconformity reduction.
TRACE
from raw materials to completed parts
MANAGE
a raw material database including metal powder, polymer coils, and more.
ADAPT
Adjust data traceability.
LEVERAGE
expertise and best practices
DEFINE
The processes and machine parameters of additive manufacturing.
CHARACTERIZE
The materials throughout every stage of transformation.
ENSURE
the privacy and security of your data.
MANAGE
Enhance finished product quality through nonconformity reduction.
TEEXMA® for Additive Manufacturing ALLOWS YOU TO:
TEEXMA® for Additive Manufacturing ALLOWS YOU TO:
R&D and project management
Establish and oversee projects for exploring the potential of additive manufacturing, while optimizing geometry, materials, and processes.
Materials and powder management
Conduct research and comparisons of material options, while effectively managing powder stock and production floor status.
Digital twin simulation
Conduct testing of build options and production samples to verify compliance with requirements, specifications, and performance expectations.
Build and sample testing
Develop, update, and oversee simulation cards to facilitate finite element analysis (FEA) and accurately predict performance using selected materials.
Build comparison and decision making
Generate and evaluate multiple builds to identify the optimal option that meets your requirements and can be implemented in production.
Order management and scheduling
Effortlessly manage quotation planning and job scheduling throughout your production floor to meet deadlines and optimize production capacity.
Build management and monitoring
Monitor and track machine settings, build status, and conditions in real-time through a user-friendly dashboard.
Quality monitoring and investigations
Capture and document sensor data to ensure adherence to quality standards and tolerances during the build process. Facilitate seamless recording of nonconformities and initiate investigations.
SOPs, workflows and equipment management
Administer operating procedures and workflows to maintain consistency across operations. Effectively schedule and oversee equipment calibration and maintenance activities to optimize uptime.
AM knowledge base & traceability
Gather valuable insights to enhance processes and improve the quality of builds. Establish digital ID cards for comprehensive part traceability throughout your entire workflow.
R&D and project management
Materials and powder management
Digital twin simulation
Build and sample testing
Build comparison and decision making
Establish and oversee projects for exploring the potential of additive manufacturing, while optimizing geometry, materials, and processes.
Conduct research and comparisons of material options, while effectively managing powder stock and production floor status.
Develop, update, and oversee simulation cards to facilitate finite element analysis (FEA) and accurately predict performance using selected materials.
Conduct testing of build options and production samples to verify compliance with requirements, specifications, and performance expectations.
Generate and evaluate multiple builds to identify the optimal option that meets your requirements and can be implemented in production.
Order management and scheduling
Build management and monitoring
Quality monitoring and investigations
SOPs, workflows and equipment management
AM knowledge base & traceability
Effortlessly manage quotation planning and job scheduling throughout your production floor to meet deadlines and optimize production capacity.
Monitor and track machine settings, build status, and conditions in real-time through a user-friendly dashboard.
Capture and document sensor data to ensure adherence to quality standards and tolerances during the build process. Facilitate seamless recording of nonconformities and initiate investigations.
Administer operating procedures and workflows to maintain consistency across operations. Effectively schedule and oversee equipment calibration and maintenance activities to optimize uptime.
Gather valuable insights to enhance processes and improve the quality of builds. Establish digital ID cards for comprehensive part traceability throughout your entire workflow.
BENEFITS
BENEFITS
Avoid Errors
Mitigate errors caused by invalid data and effectively handle preventive and corrective actions.
Streamline your additive manufacturing processes to achieve time and cost savings while maximizing production efficiency.
Reduce Costs
Interfacing
Seamlessly integrate your current information system with TEEXMA® to leverage existing data without disruption.
Enhance operational efficiency by monitoring and presenting key performance indicators (KPIs), empowering users to focus on their tasks and boost productivity.
Optimize Operations
Adaptability & Scalability
Customize and tailor your database to align with your unique business requirements and additive manufacturing (AM) processes, facilitating company growth and scalability.
Avoid Errors
Reduce Costs
Interfacing
Adaptability & Scalability
Optimize Operations
TEEXMA® for Additive Manufacturing IN VARIOUS INDUSTRIES:
TEEXMA® for Additive Manufacturing IN VARIOUS INDUSTRIES:
AUTOMOTIVE
The automotive industry has emerged as a prominent sector in the adoption of additive manufacturing, primarily to cater to rising demands and enable customized production for luxury vehicles.
Furthermore, the industry is addressing the growing environmental concerns by manufacturing lighter and more energy-efficient cars.
Consequently, there is a pressing need to carefully and strategically select and manage additive manufacturing materials like polypropylene, polyurethane, PVC, and others.
Aerospace & Defense
Additive manufacturing is gaining significant importance in advanced industries like aerospace and defense.
The industry’s demand for flexibility in response to specific changes necessitates expediting the shift from prototyping to assembly-line production.
Defense applications often involve intricate and low-volume parts, and additive manufacturing is the most effective method for producing such parts in limited quantities, while also enabling localized production.
Medical
Additive manufacturing has a significant impact on the medical field, encompassing surgical applications and medical device production.
One of the key challenges involves effectively managing the materials utilized in the final products, such as polymers, PEEK, PEKK, etc. This includes meticulous physicochemical characterization (ISO 10993) to ensure biocompatibility and minimize risks.
Additive manufacturing enables the customization of intricate parts and fosters innovation in an increasingly technology-driven sector.
Energy
TEEXMA® for Additive Manufacturing streamlines research and development (R&D) projects and promotes technology transfer within the energy industry.
Companies in this sector face the challenge of manufacturing components that optimize performance while minimizing material usage.
This challenge pertains to energy generation devices (e.g., solar panels, wind turbines) as well as energy conversion devices (e.g., batteries, generators).
AUTOMOTIVE
The automotive industry has emerged as a prominent sector in the adoption of additive manufacturing, primarily to cater to rising demands and enable customized production for luxury vehicles.
Furthermore, the industry is addressing the growing environmental concerns by manufacturing lighter and more energy-efficient cars.
Consequently, there is a pressing need to carefully and strategically select and manage additive manufacturing materials like polypropylene, polyurethane, PVC, and others.
Aerospace & Defense
Additive manufacturing is gaining significant importance in advanced industries like aerospace and defense.
The industry’s demand for flexibility in response to specific changes necessitates expediting the shift from prototyping to assembly-line production.
Defense applications often involve intricate and low-volume parts, and additive manufacturing is the most effective method for producing such parts in limited quantities, while also enabling localized production.
Medical
Additive manufacturing has a significant impact on the medical field, encompassing surgical applications and medical device production.
One of the key challenges involves effectively managing the materials utilized in the final products, such as polymers, PEEK, PEKK, etc. This includes meticulous physicochemical characterization (ISO 10993) to ensure biocompatibility and minimize risks.
Additive manufacturing enables the customization of intricate parts and fosters innovation in an increasingly technology-driven sector.
Energy
TEEXMA® for Additive Manufacturing streamlines research and development (R&D) projects and promotes technology transfer within the energy industry.
Companies in this sector face the challenge of manufacturing components that optimize performance while minimizing material usage.
This challenge pertains to energy generation devices (e.g., solar panels, wind turbines) as well as energy conversion devices (e.g., batteries, generators).